Installation Instructions for SPC Products
for Waterproof Stone Powder Composite (SPC) FloorsHemingway Collection 4.2mm | 12mil
Cosmos Collection 5.5mm | 20mil
New World ll Collection 6.5mm | 20 mil

All our click products use the patented Uniclic® system!
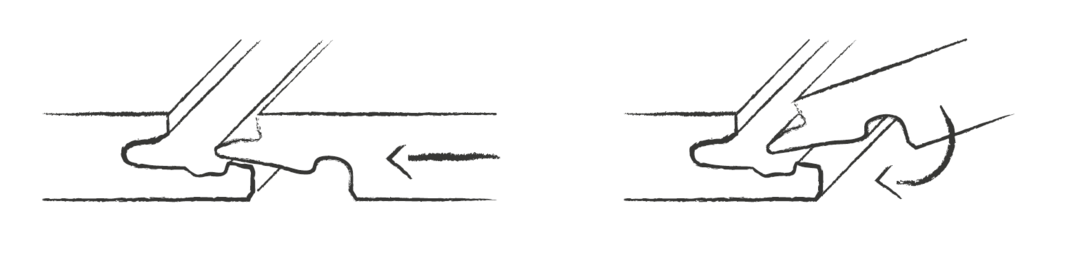
..and offer a Limited Residential Lifetime Warranty for peace of mind.
HEMINGWAY 4.2mm, 12mil SPC
Known for being the most waterproof LVP on the market, our signature SPC’s rigid core is virtually indestructible, making it an ideal for high-traffic and commercial environments.
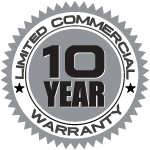
COSMOS 5.5mm, 20mil SPC
The newest addition to our SPC collection brings the best of both worlds with extra thickness, added length, a 20yr commercial warranty and new color ways.
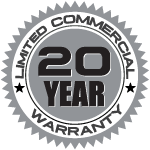
NEW WORLD II 6.5mm, 20mil SPC
An upgrade to our thickest and widest SPC features a UniClic locking system, lifetime residential warranty, more colors and a 1.5mm IXPE 2 in 1 pad.
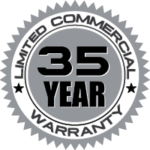
Aperion Surfaces SPC floors are durable and backed by industry standard warranty coverage. With proper job site preparation, installation, and routine care and maintenance, your new floor will give you years of beauty and function. The Aperion SPC features an attached underlayment pad that is designed for a floating installation method and can be installed over existing floors provided they meet subfloor requirements listed below. The flooring is intended for interior use only and is suitable for above-grade, on-grade and below grade applications. The floors should not be installed in locations where the substrate below the building structure is exposed to the elements or where there are structural problems related to ongoing moisture exposure.
INSTALLER/OWNER RESPONSIBILITY Please read these instructions and warranty disclosures completely before proceeding to installation!
SPECIAL NOTE: Flooring MUST be glued down for heavy rolling loads such as hospital beds, chair casters, carts, wheelchairs, etc. It is not suitable for these uses without adhesive.
BY INSTALLING THIS PRODUCT, YOU ASSURE THAT ALL INSTALLATION REQUIREMENTS OUTLINED HERE HAVE BEEN MET AND AGREE TO THE TERMS AND CONDITIONS OF THE APERION SURFACES LIMITED WARRANTY.
Product Handling & Inspection
Always transport and store the SPC planks carefully to prevent damage. Store on a flat surface. Do not store boxes upright on their ends or in areas subject to extreme temperatures.
IT IS THE INSTALLER/OWNERS RESPONSIBILITY TO DO A FINAL INSPECTION OF THE FLOORING PRIOR TO INSTALLATION. This inspection should include product color, quality, finish and locking system. Aperion Surfaces will not accept responsibility for the installation of any flooring planks with visible manufacturing defects. If the product is not acceptable, DO NOT PROCEED WITH THE INSTALLATION. Do not continue opening cartons and do not discard cartons that were opened during inspection. Contact your Aperion Surfaces retailer immediately for assistance.
INSTALLATION GUIDES
Jobsite Preparation Exterior Structural damage caused by water and/or high humidity must be resolved prior to installation. Ensure that exterior grading is complete with surface drainage offering a minimum drop of 3″ in 10′ to direct exterior water sources away from the structure where the flooring will be installed inside. Crawl spaces should be a minimum of 18″ high, insulated per latest building code requirements, with a minimum 6-mil ground cover vapor barrier. Crawl spaces should offer cross-ventilation air vents equivalent to at least 1.5% per 100 square feet of floor space. Interior Moisture issues must be detected and corrected before installation. Aperion Surfaces SPC floors are waterproof but are not intended for use as a moisture barrier. A minimum 6-mil vapor barrier is required over all concrete and gypsum applications.
The jobsite should be enclosed, and climate controlled prior to installation. HVAC systems must be fully operational with a consistent room temperature of 55°- 85° F and relative humidity levels of 35%-55% before the flooring is delivered or installed, and throughout the lifetime of the flooring installation.
Do not install Waterproof floors where they will be subject to extreme hot or cold temperatures at any time. Do not install cabinets or heavy fixtures directly on the flooring.
Subfloor Conditions
The quality and preparation of the subfloor over which your SPC / ESPC floor will be installed is critical to a successful installation. Wood subfloor seams should be sanded flat. Concrete floors should be ground or patched to a suitable flatness of 3/16” in 10’
Acceptable Subfloor Types
- CDX Plywood
- Concrete. Minimum compression strength of 3000 PSI
- OSB/Particle Board
- Existing resilient tile, sheet vinyl (one layer) or ceramic tile Minimum subfloor requirements for all installations:
- Structurally sound, smooth, clean and free of debris, including but not limited to, staples, nails, wax, grease, paint, sealers and old adhesives.
- Level and flat to 3/16″ per 10′.
- Dry throughout the lifetime of the installation.
- Wood subfloor must be:
- Tested for moisture not to exceed 11%.
- Nailed or screwed down every 6 inches along the joists to remove subfloor squeaking.
- Leveled with high spots sanded down and low spots filled with a leveling compound.
- Leveling material should provide a structurally sound wood subfloor
- Concrete subfloor must be:
- Fully cured for at least 60 days prior to installation.
- Tested for relative humidity, moisture and pH. Relative humidity tests should not exceed 85% (RH); Calcium Chloride Test for moisture should be no more than 8lbs per one-thousand square feet in 24 hours MVER (Moisture Vapor Emission Rating) and pH tests for alkalinity levels should register between 7 and 9.
- Installed properly with a minimum 6-mil poly film moisture barrier between concrete and ground below.
- Resilient tile, sheet vinyl or ceramic tile requirements:
- No more than one layer.
- Well secured to the structural subfloor.
- Grout lines of any depth should be filled in with a cementitious leveling and patching compound to assure a smooth, flat surface.
- DO NOT INSTALL THE SPC OVER CUSHION BACKED GOODS OR ANY OTHER FLOORING THAT IS NOT COMPLETELY ADHERED TO THE SUBFLOOR.
Floor coverings that must be removed prior to the SPC flooring installation include:
Carpet, needle felt, cushion vinyl, floating floors of any kind; parquet, solid and engineered hardwood over concrete; sleeper substrates. Do not install over existing wood flooring glued to concrete.
Radiant Heat Guidelines for the SPC
The flooring should only be installed over embedded radiant heat flooring systems. Prior to installation, the radiant heating system should be operational with the heating temperature set to 68°F 48 hours before, during and 72 hours after installation. The temperature of the radiant heating system may be increased gradually 72 hours after installation, but the surface temperature should never exceed 85°F
Installation Tools generally needed: Spacers, Hammer, Tapping Block, Pencil, Tape Measure, Utility Knife
Aperion Surfaces floors are designed to replicate the look of a real wood product with natural variations in color, texture and grain. For optimal visual effect, shuffle planks from several cartons and avoid installing similar planks nearby one another. For aesthetic purposes, plank flooring is often laid in the direction of the longest wall. It is the responsibility of the installer/owner to make the final decision regarding which direction the planks will run. The SPC flooring must be installed in a staggered fashion to achieve an overall random appearance with the stagger being no less than 8”.
- Installations with runs exceeding 40’ should be broken with a molding if possible
- Commercial installations require a T-Mold / break in all doorways less than 6’
Starting Installation
Select installation starting point next to an outside wall. This is usually the straightest and best reference for establishing a straight working line. Establish the working line by measuring an equal distance from the wall at both ends and snapping a chalk line. The distance you measure from the wall should be the width of a plank. You may need to scribe cut the first row of planks to match the starting wall in order to make a straight working line if it is out of square. Undercut or notch-out door casings to fit flooring thickness by placing a piece of flooring on the subfloor as a height guide for sawing. Remove door thresholds and base moldings and replace after flooring installation. Always leave at least 1⁄4″ expansion space around the perimeter including adjacent existing flooring or other structures such as hallways, door jams and thresholds. For the best visual effect, planks in the final row of the installation area should be at least 1⁄3 the width of a full plank. Measure the room at a right angle to the direction of the flooring, calculate the number of planks required to fit, and, if necessary, cut plank widths in the first row to a smaller size. You may want to position a few rows before starting installation to confirm your layout. When laying flooring, stagger plank end joints row by row by at least 8″. You can use the cut-off end to begin the next row when cutting the last plank in a row to fit. If the cut-off end is less than 8″, discard it and instead cut a new plank at a random length (at least 8″ in length) and use it to start the next row. Always begin each row from the same side of the room and ensure that minimum 1⁄4″ spacers are placed at ends and edges where planks meet the wall. The tongue side of the plank should face the starting wall.
As installation proceeds, cut the last plank in each row allowing for the min required 1⁄4″ expansion space, and continue to check that both long edge and end joints are locked, secure and have not shifted during this process.
As installation proceeds, the installer/owner should inspect and approve each piece that will be used in the flooring installation. The installer must use reasonable selectivity and hold out or cut off pieces with defects that do not fall within manufacturing tolerances whatever the cause may be. Aperion Surfaces will not honor claims due to a lack of on-site flooring inspection and acceptance by the installer/owner.
FLOOR CARE & MAINTENANCE
SPC floors are durable, but like all interior floor coverings require care periodically to look their best and prevent problems before they occur. The frequency will depend on your lifestyle and traffic on the flooring over time.
Routine & Preventive Care Do’s and Don’ts
- Sweep, dust mop or vacuum (air suction only) regularly to remove loose dirt and grit. Do not use treated dust mops.
- Do not use a steam cleaner on the SPC floor.
- Clean up spills or pet accidents immediately.
- Avoid exposure to long periods of direct sunlight. Close blinds or drapes during peak sunlight hours. SPC flooring subjected to excessive heat and light is subject to thermal degradation.
- Maintain consistent room temperature of 65°- 85° F and relative humidity levels of 35%-55% at all times.
- Do not expose the SPC flooring to temperatures exceeding 110° or temperatures below 32°F.
- Ensure that chairs or furniture with casters or wheels are easy swiveling with large surface non-staining casters and suitable for resilient floors use. Do not use ball type casters as they can damage the floor.
- Protective mats and chair pads are required under office chairs or furnishings with rolling casters.
- Ensure that frequently moved furniture is protected with felt pads to avoid scratching the floor. Heavy furniture and appliances should be equipped with non-staining large surface floor protectors. Use floor protectors under furniture.
- Use mats at entrances to prevent dirt and grit from being tracked on to the floor.
- Protect flooring in the kitchen area with a high-quality rug in areas subject to hot oil spills or splatter.
- Use non-staining mats only. Rubber may discolor the floor.
- Do not use electric brooms with hard plastic bottoms without padding as these may damage the flooring.
EXCLUSIONS
The following are not covered by this Limited Warranty:
- Damage due to improper job site preparation and/or subfloor conditions, installation or maintenance. · Damage caused by failure to properly line up end joints during installation.
- Damage caused by pet accidents.
- Damage caused by excess moisture in concrete subfloor.
- Damage caused by fire or burns, accidents, intentional abuse, flooding, construction or installation.
- Damage caused by vacuum cleaner beater bar; indentations or damage caused by improper rolling loads, caster wheels, chairs or other furniture without proper floor protectors and cuts from sharp objects.
- Surface scratches or scuffing.
- Changes in color or sheen due to exposure to sunlight or due to use of rubber-backed mats.
- Exterior or non-flooring applications.
- Loss of gloss.
- Minor shading, color or texture differences between samples or printed color photographs or illustrations and delivered product.
- Damage due use of adhesives or tape; exposure to acetone or other harmful chemicals; punctures, cuts, indentations; failure to use protective mats under heavy and/or rolling furniture, including but not limited to, desks, desk chairs, exercise equipment.
- Flooring sold as irregulars or trial grade materials or “as is”.
- Product installed in locations subject to heavy static loads, heavy rolling fixtures and/or furniture, including but not limited to, areas of recreational, hospital or rehabilitative activities.
- Product installed in commercial food preparation areas and underneath food preparation tables.
- Improper use of the flooring product to seal an existing floor from moisture. Aperion Surfaces SPC is a waterproof floating floor that comes with an attached underlayment pad, but is not intended to act as a moisture barrier.
- This Limited Warranty is void if, prior to installation in commercial and light commercial applications this flooring is not acclimated to room temperature (between 65°F and 85°F) at the job site for a minimum of 24 hours and, if post installation (in all applications) such flooring is not continuously maintained at such temperature.
- Only installation techniques described in the Hemingway, Cosmos and New World II Installation & Maintenance Guide are warranted.
- Aperion Surfaces SPC installations involving custom cutting, such as 45-degree mitered corners and serpentine edges.
- Loss due to loss of time, inconvenience, incidental expenses (such as telephone calls, labor and/or materials) incurred in the removal or re-installation of the affected material, and any other incidental or consequential damages.
CUSTOMER SERVICE & CLAIMS
Internet Sales Policy
The Aperion Surfaces manufacturer warranty applies only when the Aperion Surfaces SPC flooring purchase is made directly through an authorized Aperion Surfaces flooring dealer. Online sales of Aperion Surfaces SPC flooring products are not covered by the manufacturer warranty. Any Aperion Surfaces SPC flooring sale that has been misrepresented by the retailer/seller, including but not limited to, returns, off-color, or manufacturer defect resale, are not covered by the manufacturer warranty.Claims Process
All claims must be filed within the warranty coverage period and go through the flooring retailer where the flooring was purchased. The original purchase receipt must be submitted with the warranty claim. Aperion Surfaces reserves the right to have an Aperion Surfaces representative inspect the floor, remove samples for technical analysis and request proof that pre-installation, installation and floor care and maintenance are in accordance with Aperion Surfaces requirements. If any portion of your floor should fail with respect to applicable warranty provisions, Aperion Surfaces will repair, refinish or replace the product at its sole discretion. Should you have any questions or concerns regarding your flooring, please contact Aperion Surfaces 201-962-2090
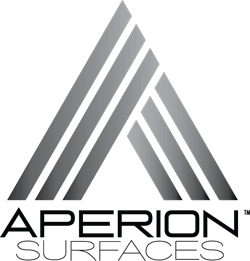
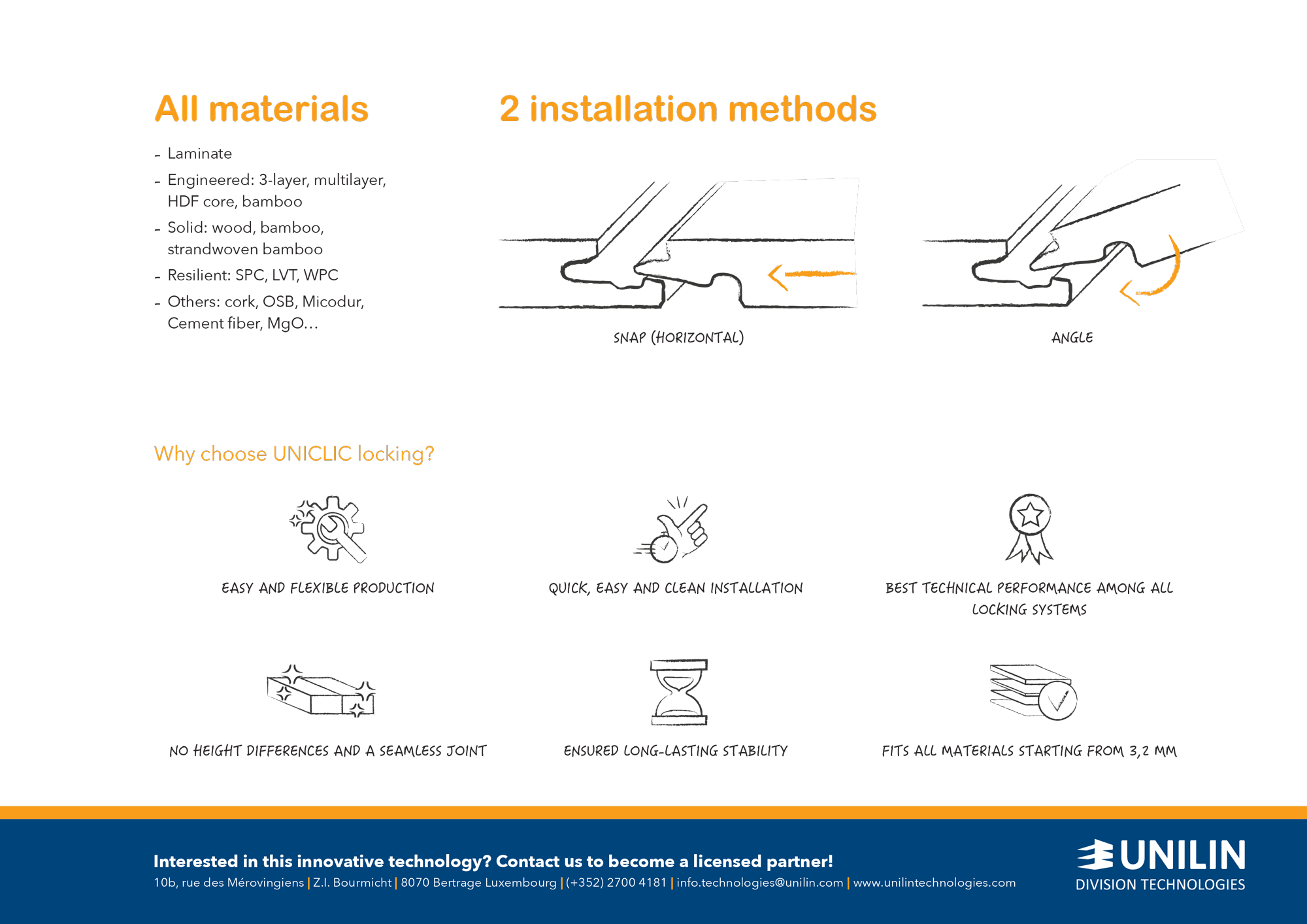
Touch base and learn about the value we can provide your building or project!
Let’s Talk Surfaces
Main: (201) 962-2090
90 Boroline Road
Allendale, NJ 07401
info@aperionsurfaces.com
8am-5pm